Videos
Loading the player ...
- Offer Profile
- The BEUMER Group is an
international leader in the manufacture of intralogistics for conveying,
loading, palletising, packaging, sortation and distribution technology.
Product Portfolio
Conveying Technology: ALWAYS IN MOTION EVERYWHERE
-
BEUMER has been a supplier of systems and equipment for the
transportation of bulk and piece goods around the world for many
years. With success. Whether for the cement, lime or gypsum
industries, for the chemical industry or for new markets such as the
energy sector, BEUMER belt conveyors, conveyors for hot materials
and high-capacity bucket elevators always offer the ideal solution
for your specific transportation requirements.
IMPRESSIVE CONVEYING TECHNOLOGY: EFFICIENT AND SAFE
Long distances, extreme heights, high temperatures - the range of
custom system solutions from BEUMER Group is as broad as the range
of requirements in the conveying technology sector. Thanks to our
vast technical expertise, we always find the right way to transport
your products quickly, safely and efficiently from A to B.
AT A GLANCE:
- Belt conveyors as closed (pipe conveyors) or open conveyors
and in curved configurations
- High-capacity bucket elevators as belt and chain bucket
elevators
- Hot material conveyors as apron conveyors with link plate
chains or steel cable belts
- Charging, metering and shut-off equipment
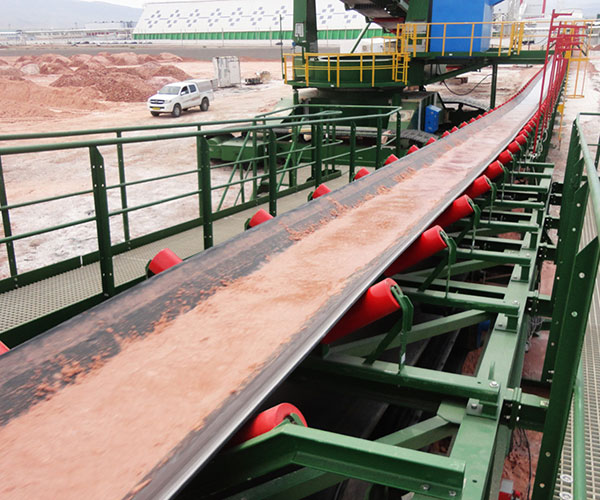
Belt Conveyor
-
EFFICIENT SOLUTION FOR LONG DISTANCES
Pioneer with know-how.
For many years BEUMER Group has been successfully supplying systems
and plants for bulk material and piece good transport worldwide.
Since its foundation BEUMER Group has substantially shaped technical
development in the conveying technology sector and, with its belt
conveyors, can always offer you the right solution for your
transport requirements.
AT A GLANCE:
- Centre distance:
- BEUMER troughed belt conveyors: up to 20 km
Curve radius:
- BEUMER troughed belt conveyors: > 400 m for horizontal curves, vertical curves depending on the application
Conveying capacity:
> 10,000 t/h
Conveying speed:
up to 6.5 m/s
Angles of inclination:
up to 15° depending on the material to be conveyed
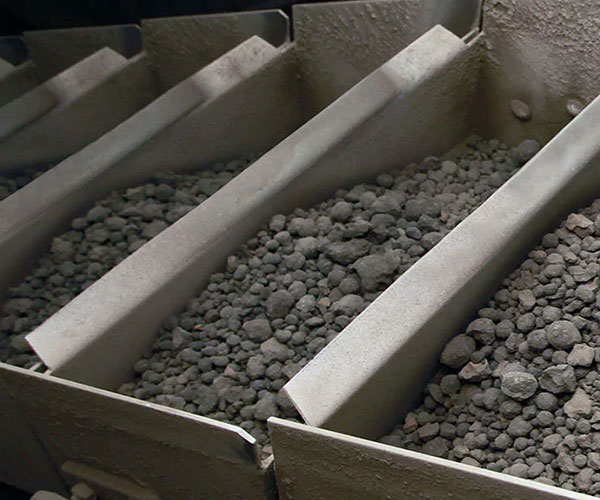
Apron conveyor
-
THE ‘HOT STUFF’ OF CONVEYING TECHNOLOGY
High temperatures, complex configurations, overcoming extreme
heights - thanks to a comprehensive product range, BEUMER apron
conveyors are ideally matched to the special demands involved in the
transportation of hot materials.
The tried-and-tested mechanical components of apron conveyor
technology are the basis for extreme reliability and problem-free
operation. The use of highquality construction materials in
combination with technologies developed down to the last detail and
manufacturing precision ensure a long service life and guarantee
significant economic benefits.
AT A GLANCE:
- Cell widths up to 2,000 mm possible
- Angles of inclination up to 45° possible
- Conveying speed with a chain traction element: up to 0.3 m/s
- Conveying speed with a belt traction element: up to 0.6 m/s
- High flexibility
- Tailor-made solutions for every application
- Wide product range possible
- High economic efficiency with little capital investment
- Low-wear design for high durability
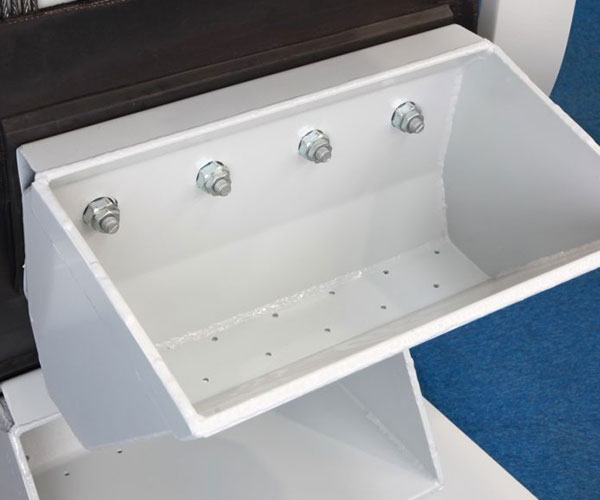
Bucket elevators
-
HIGH-CAPACITY
Bucket elevators have proven themselves for vertical transport of
many and diverse bulk materials for decades. As a market leader,
BEUMER Group successfully established the belt bucket elevator
technology in the market decades ago.
Belt bucket elevators were consistently developed in the past and
enable the highest possible conveying capacities with maximum centre
distances today.
Chain bucket elevators are the preferred conveying systems for the
transport of hot bulk materials and coarse-grained materials. With
its central chain bucket elevators, BEUMER Group offers efficient
and proven solutions even for the highest conveying capacities.
AT A GLANCE:
- Large conveying heights > 175 m are feasible
- Conveying capacities of up to 1,800 m3/h are possible
- Maximum wear resistance even with highly abrasive materials
- Transport of high-temperature bulk material
- Special versions for ATEX requirements or for similar applications in potentially explosive areas are possible
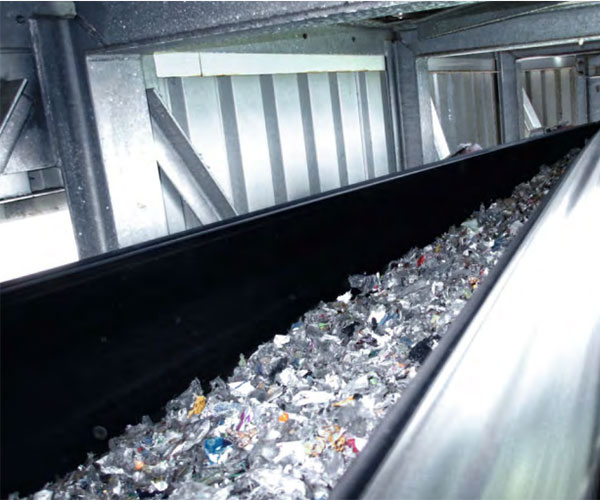
Pipe Conveyor
-
The Pipe Conveyor is an enclosed curve going transportation system
for all kinds of bulk materials. At the loading and discharging
points, the conveyor system is identical with open troughed
conveyors. The difference starts after the loading point, where the
belt is formed into its typical tubular shape by special idler
arrangements over a certain distance and finally is led through
idler panels with hexagonal cut outs and offset idler arrangement.
At the discharging point, the belt opens automatically after the
final idler panel and transfers the material to its next
destination.
AT A GLANCE:
Technical Facts:
- Pipe diameters between 150 and 650 mm
- Centre distance up to 10 km
- Curve radius depending on material and topography:
- min. 300 x diameter for fabric belts
- min. 600 x diameter for steel wire belts
- Angles of inclination up to 30° depending on the material to be conveyed
- Advantages:
- Protection of the conveyed material against external influences
- Protection of the environment against escaping material by dustfree transport
- Possibility of tight curve radii
- Realization of steep inclination
- Low space requirements
- No need for transfer towers
- Adaptation ability to topographic requirements
- Possibility of downhill transportation
- Simultaneous double load transport of different kinds of material in the upper and lower strand
- Low investment costs
- Low maintenance costs
- High operational safety
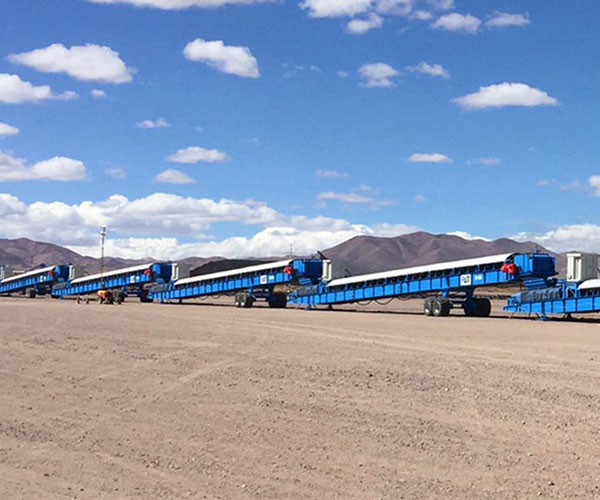
Alternative fuel handling
-
The required energy input causes about 40% of the production costs
for the manufacture of cement. Therefore apart from standard
combustibles like coal, fuel oil and gas the so called alternative
fuels are of considerable interest, besides a useful waste disposal
their utilization offers important economical advantages.
The BEUMER Group system technology is designed to meet these
particular demands of construction and functionality. Due to the
modular design of all construction groups and system components,
each project can be individually planned with regard to capacity
requirements.
For more than two decades BEUMER Group has gained experience in the
development of systems for the burning of secondary fuels and during
this period a large number of projects has been realized. Knowledge,
supplies, and engineering services are part of the support when
dealing with BEUMER Group. Experience as well as the continuous
development in the field of the energetic utilization of solid waste
fuels have led to the demand for an exploitation of all products
offered in this market.
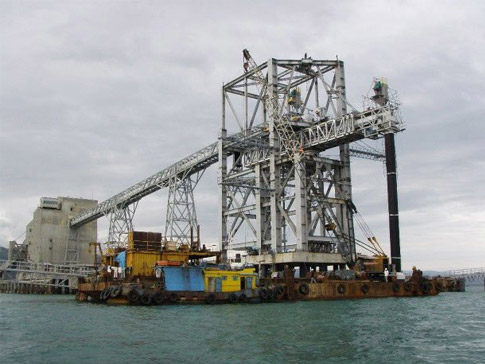
Ship Loading
-
Entire port terminals or a single barge loader – BEUMER offers the
complete range of required equipment for your industry: mining,
cement, power, chemical (fertiliser) and food (grains). Besides the
conveying technology, BEUMER can supply the ship loading technology
best suited for your task, be that a quadrant-type ship loader, a
travelling ship loader with luffing and slewing gear or a barge
loader with a telescopic conveyor.
A ship loading system must provide fast ship turnaround, while at
the same time being environmentally friendly, creating no spillage
and minimal dust emissions. It has to accommodate the space
requirements of the jetty, allowing movement of trucks and other
vehicles, as well as different types and sizes of ships. It must
also handle the requirements of the conveyed material. With BEUMER's
modular design it is possible to provide tailored concepts.
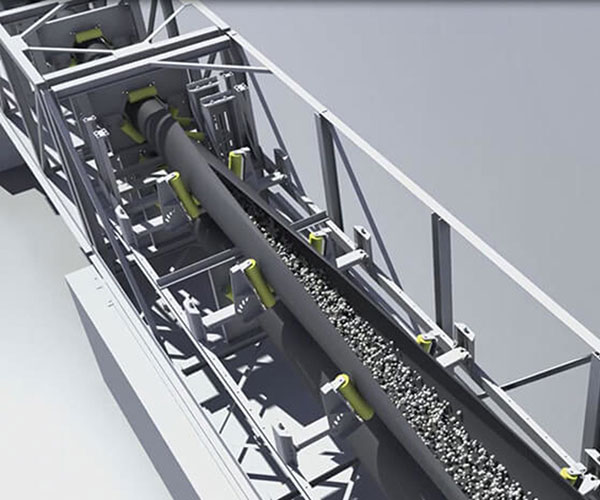
Storage & Blending Bed
-
From single buffer storages and blending beds to complete bulk
terminals, BEUMER offers the complete range of required equipment
for your industry: mining, cement, power, chemical (fertiliser) and
food (grains). Besides the conveyor technology, BEUMER can supply
the stackers and reclaimers best suited for your Task..
Based on the specific task (buffering, collecting and distributing,
blending/homogenising) and the resulting incoming and outgoing
material flow, first the storage capacity is decided upon. Together
with the material properties this then leads to a choice of
available stacking and reclaiming methods as well as the two basic
stockpile layouts, namely the longitudinal stockpile arrangement and
the circular stockpile arrangement.
Loading Technology: PRECISE, SAFE AND CLEAN
-
We provide the perfect solution for loading and unloading any
vehicle, from trucks to railway cars to ships. At the centre is the
actual loading machine. From there, we design, manufacture and
install entire loading systems, tailor-made to your requirements and
the products to be conveyed.
Our loading technology provides economic efficiency, easy operation
and high capacity. We have pioneered in this field for decades. Our
loading technology portfolio includes:
- systems for loading loose or bagged bulk material into trucks, waggons, and ships
- unloading machines
- automatic bag loading machines for trucks and containers
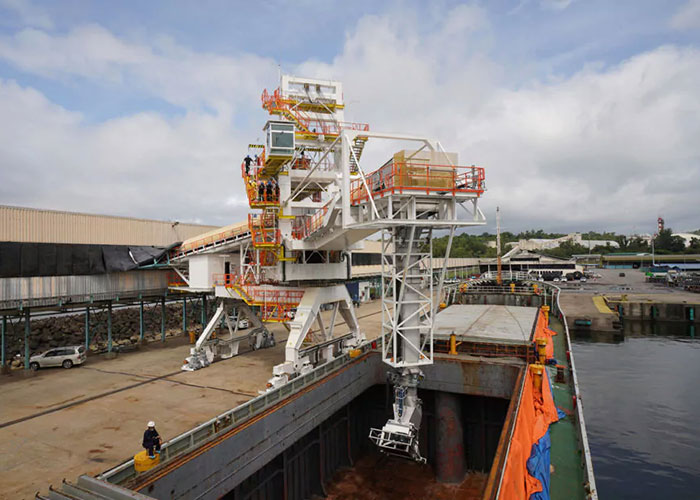
Bulk material
-
Efficient, reliable and safe bulk material transport
The right loading technology is crucial for efficient and safe
delivery of your products to your customers: We are one of the
leading providers of systems for bulk material loading. We offer our
customers a high degree of availability and economical operation
through our many years of experience, high-quality products,
extensive know-how and the continuous development of the loading
technology for bulk material.
Product overview of our loading technology for bulk material
Bulk loading heads:
- for bulk transporter vehicles
- with an integrated filter
- with fill level indicator
Loading systems:
- for bulk transporter vehicles
- for open vehicles
- for trains
- for ships
- dispatch automation
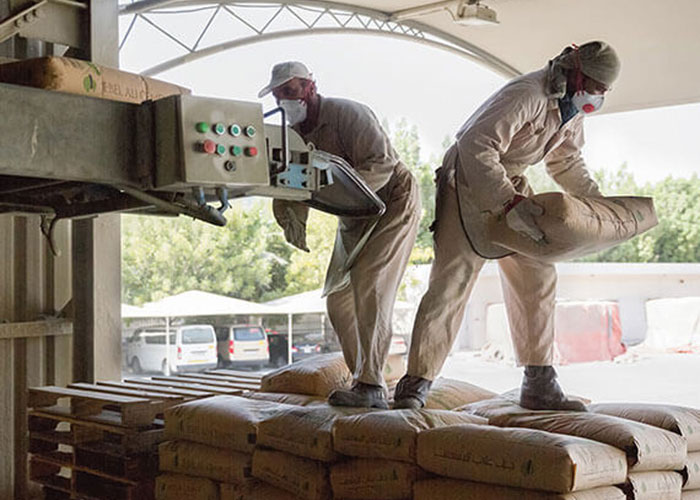
Bag loading
-
The concept of the three dimensionally adjustable bag loading machine
with telescoping head for loading trucks and railcars can be traced
back to a German patent issued to BEUMER Group several decades ago.
In the meantime, BEUMER Group has supplied many loading machines,
both standard and special models, for road and rail vehicles and, in
addition to supplying individual machines, has equipped various
packing plants worldwide with such equipment. Mechanized and semi-
or fully automatic bag loading equipment has become a BEUMER Group
speciality. Bag transport equipment, bag cleaners and devices for
rejecting broken bags as well as the system controls expand the bag
loading equipment into complete installations.
The BEUMER autopac® 3000 is an economic and efficient system for
simultaneous loading and palletising of bagged material, such as,
cement, lime, gypsum, grain, flour, sugar, plastic granules, food
and fertilisers, or similar products. The BEUMER autopac® 3000 is
available in mobile and stationary designs and is therefore suited
for various applications. These alter - native designs allow an
optimum utilization of the dispatch capabilities. Loading and
palletising as one operation - this is the proven BEUMER autopac®
3000. Open trucks are automatically loaded with bags directly from
the packer onto the loading layers at an hourly capacity of 3.000
bags.
The BEUMER autopac® 3000 is moved into its initial loading position
by remote control. The number of rows and layers as well as the
total number of bags are stipulated. The reafter loading runs
automatically. The BEUMER autopac® 3000 is constructed entirely of
electro - mechanical components. The drives and machine parts are
clearly arranged and easily accessible. This design offers decisive
advant - ages even under extreme ambient conditions through its high
availability and outstanding efficiency in operation.
Filling Technology
-
Filling technology for building materials, cement and chemicals
As an expert in filling technology, BEUMER Group is the reliable
partner you need. BEUMER systems are used for reliable, gentle and
sustainable bagging of building materials, cement and chemicals.
Processes that work perfectly together ensure optimal performance at
all times. BEUMER Group stands for accurate engineering – driven by
visions, realised with precision.
Highlights
- Primary packaging for the building materials, cement, mineral and chemical industry
- Low initial costs
- High parts availability
- Easy to maintain
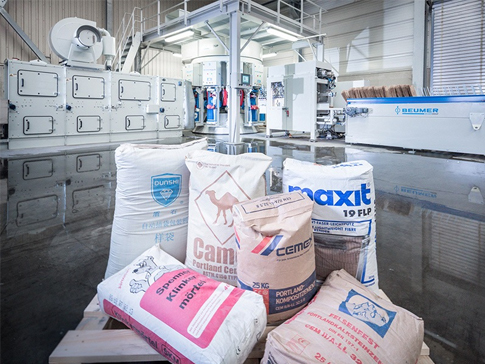
Fillpac
-
The BEUMER fillpac® I (in-line packer) and the BEUMER fillpac® R
(rotary packer) are a new generation of bagging systems - a first
class system with the world's latest microprocessor for weighing
electronics, proven filling systems with horizontal filling
impellers, and precise weighing accuracy. The BEUMER fillpac® is
designed for capacities ranging from 300 to 6000 bags per hour.
In-line as well as rotary packers are available as per customer
requirements.
Best results with performance and weighing accuracy due to:
- simple, graphical programming interface, which can be operated using a touch screen
- different filling weights that can be stored in the database and are selectable using a selector switch
- simple calibration using softkeys on the touch screen
- autocorrections, with which the maximum weight accuracy and fill speed can be achieved
FEATURES
Horizontal filling impellers are used for the BEUMER fillpac® in
order to ensure trouble-free filling.
The EFS100TS electronics were designed in Europe, are being
continuously developed further and fulfil the sophisticated demands
of efficient and modern bagging systems.
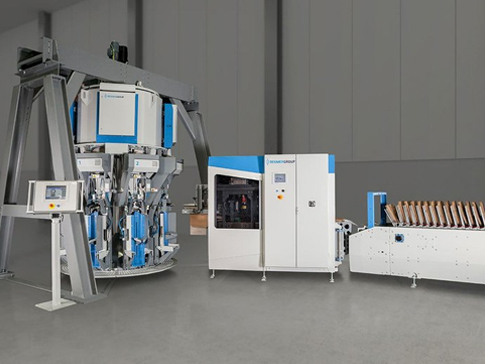
Fillpac RH/RV
-
ROTARY FILLING
Turbine filling machine for high throughput
Whether cement, limestone or diverse types of plaster– the
high-performance BEUMER fillpac® RH/ RV rotary impeller filling
system cleanly, accurately and reliably fills up to 260 tonnes of
finegrained materials per hour into various bag sizes. Bags with a
length of up to 800 mm can now also be filled. A high-performance
drive increases the availability of the turbine filling machines.
Even materials which are difficult can be reliably processed. The
new design improves the material flow through the filling spouts.
Highlights
- Filling of various bag variants with a length of up to 800 mm
- Optimised material flow thanks to high-performance filling impeller drives
- Simple set-up and reproducible nozzle adjustment
- Service-friendly accessibility and simple retrofitting and conversion thanks to true modularity
- Accurate filling thanks to tried and tested weighing technology
- Simple, intuitive operation via HMI (Human Machine Interface)
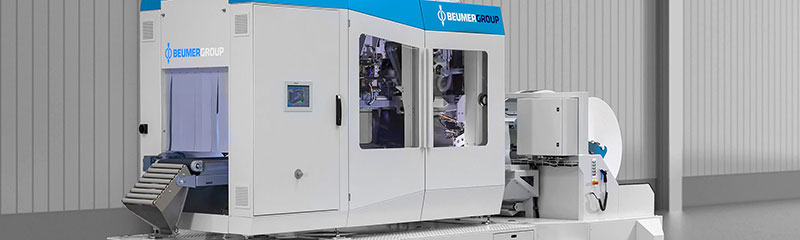
Fillpac FFS
-
INNOVATIVE FORM FILL SEAL SYSTEM FOR CHEMICAL PRODUCTS
Reliable, gentle and sustainable filling
High product temperatures, special flow characteristics and low
dimensional stability – these are some of the challenges when
bagging and packaging chemical and petrochemical products. As a
partner of chemical companies, BEUMER Group has developed an
innovative, compact high-precision form fill seal system (FFS
system) to address these challenges: BEUMER fillpac® FFS.
Three functions in one
The BEUMER fillpac® FFS fulfills three functions with one compact
and space-saving system: It forms bags from a prefabricated tubular
PE film and fills them with the corresponding product and seals bags
at a capacity of 2,600 bags per hour. The filling process is carried
out reliably, gently and sustainably. Moreover, an integrated
weighing unit ensures exact filling results.
Highlights
- Bag forming, filling and sealing in one system
- Capacity of up to 2,600 bags per hour
- Compact, space-saving design
- Robust low-vibration technology
- Intuitive operation with an ergonomic control panel (HMI)
Palletising Technology
-
PRECISE, EFFICIENT, RELIABLE
For more than 40 years, BEUMER Group has designed and developed
innovative palletising technology for various products. Whether for
the building materials, cement, chemical or food and animal feed
industries – BEUMER palletisers feature first-class stack quality
and high reliability.
Highlights
- Graduated and comprehensive product range consisting of high-level and robotic palletisers
- Maximum capacities of up to 5,500 units per hour
- Simple upgrade due to modular design
- More than 40 years of experience in designing, developing and installing high-capacity palletisers
- BEUMER palletising technology offers substantial programs for all common packing patterns and pallet sizes. At the touch of a button, the systems can be flexibly adapted to any size or material change.
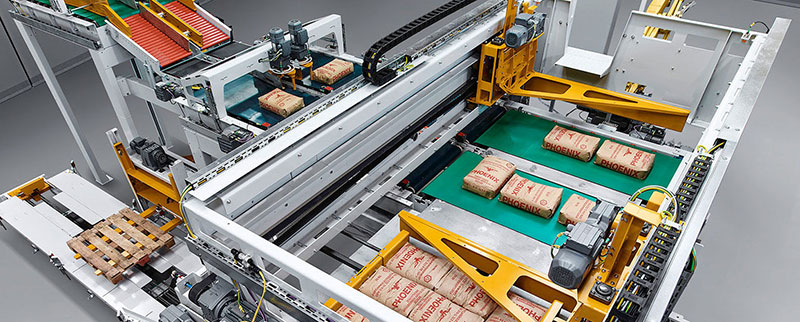
High level palletising
-
BEUMER paletpac® high-level palletisers fulfil the requirements of
various industries. The BEUMER paletpac® is particularly suited for
the gentle palletising of highly sensitive bagged products in the
lower capacity range. BEUMER paletpac® high-capacity palletisers are
used for gentle, safe and efficient palletising of robust bagged
products in particularly high quantities.
Highlights of BEUMER paletpac® series
- Gentle handling of bags
- Precise stack formation
- Programs for all common packing patterns
- Intuitive adjustment of the parameters for variable bag and pallet sizes
- Simple handling
- Low-noise and low-wear drive systems
- Compact, container-optimised
- Easy maintenance due to improved accessibility
- Performance range for sensitive goods: 600 to 2,500 bags per hour
- Performance range for robust goods: 1,800 to 5,500 bags per hour
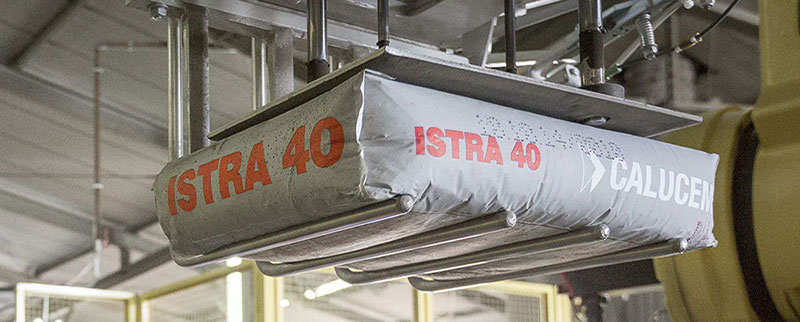
Robotic palletising
-
INNOVATIVE PALLETISING TECHNOLOGY
In many industries, not only bagged goods need to be palletised, but
also cartons, cardboard boxes, crates or canisters. BEUMER Group has
developed flexible robotic palletisers with gripper elements to meet
the different requirements of these items. The BEUMER robotpac®
series ensures firstclass stack quality, gentle product handling and
high reliability.
Highlights of BEUMER robotpac® series
- High flexibility for various tasks
- Little floor space required due to compact design
- Exchangeable grippers for picking up various packaged goods
- Simple change of the packing pattern – at the touch of a button or fully automatic through barcode recognition
- Up to 1,900 units per hour, depending on the model
- Reliable, even under extreme conditions
Packaging Technology
-
SOLUTIONS MADE BY BEUMER GROUP
3 Keys to better end-of-line packaging health.
The end of a packaging line is the beginning of a new journey for a
company's product - a journey through complex distribution channels
carried out via multiple modes of transportation. Filled with risk,
this journey carries the potential for significant but avoidable
costs and unfavorable impacts to a business and to its customers. 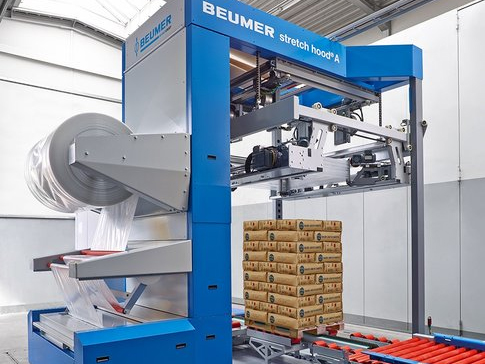
Stretch Hood® A
-
Practical, efficient and space-saving packaging technology
How do you find an even more economical way of hooding palletised
goods? By using the highly efficient and compact BEUMER stretch
hood® A from the high-capacity BEUMER stretch hood® packaging system
model range. It impresses with improved system performance,
ergonomic operation and a space-saving format. This is BEUMER's new
response to the increasing demand for machine safety and economic
efficiency in the packaging industry.
Highlights
- Space-saving design, without a maintenance platform or stairs
- Operator workplace at floor level featuring optimum ergonomic design
- Easy and direct insertion of the film with a film transport system that is gentle on the film
- No cooling time required for the film sealing seam
- Energy-saving drive technology
- Intuitive operation via a soft-touch panel
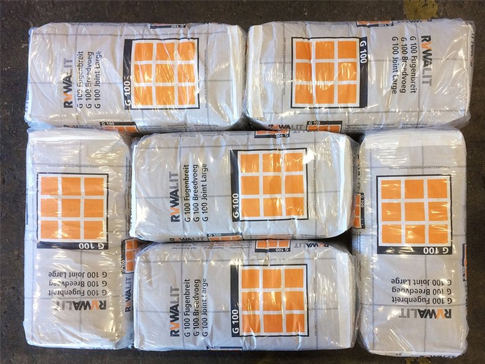
Bag-in-Bag Film Packaging
-
Weatherproof packaging for high-level product protection
The new BEUMER bag-in-bag® is the ideal addition to existing filling
and packaging systems. This procedure permits packaging paper bags
after filling – either individually or in multiples – quickly and
reliably in a weather-resistant plastic film. This ensures that your
products are perfectly protected against moisture, dust, insect
infestation and other environmental factors when they are
transported or stored.
Highlights
- Environmentally friendly production
- Use of thin films for optimised material utilisation
- Weather resistance for high-level product protection
- Simple retrofitting of existing systems
- Can be individually combined with existing filling systems for optimum flexibility
- Increased filling capacity
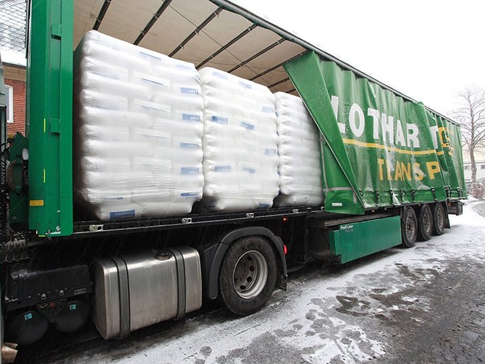
Palletless Transport
-
PACKAGING SOLUTIONS
MADE BY BEUMER GROUP
Doing more with less has driven BEUMER Group since decades -
Reduction is good but sometime eliminating is better and leads to
real eco effectiveness. BEUMER Group focuses first on listening.
Always. Listening to our customers' voices, and even going farther
downstream to listen to their customers' voices.
Then we focus on innovation that makes a meaningful difference at
the point-of-impact.- where it really matters to end users of the
broad range of industrial and consumer products that are processed,
converted, or handled in some form by BEUMER Group technology.
Taking the decision to go pallet less should be reviewed under the
perpective of creating a logistically manageable load. Should your
distribution chain meet those requirements you could benefit from:
- Significant reduction of CO2 emissions due to reduced transportation efforts (weight, increased utilization of container or trucks, eliminating of empty pallet transport, etc.)
- Improved hygiene
- 6 sided environmental protection
- Reduced handling
- Use of recyclable materials
- Less onsite storage required
- Increased system reliability
- Our goal is to improve the use of recyclable materials and to re use them within the packaging material chain according to the cradle-to-cradle principle. With the BEUMER Group palletless approach we not only want to do things right, we want to do the right things.
Airport Baggage handling systems
-
The BEUMER Group provides fully integrated automated high-speed
airport baggage handling systems for small, medium, and large
airports worldwide. This includes producing and integrating systems
for security screening, storage, sortation and transportation of
departure baggage from check-in to departure gate, as well as
transportation of transfer and arrival baggage.
Our solutions are tailor-made according to the specifications of the
client and include the entire process from concept analysis and
design to long-term service & support including operations and
maintenance. 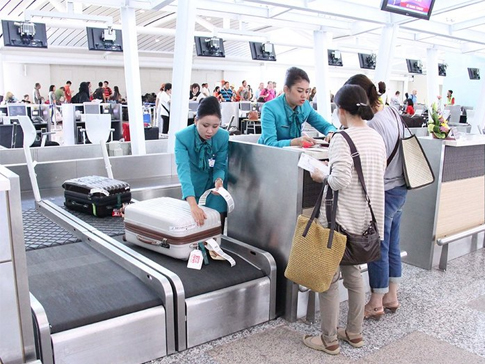
Check-in systems
-
Check-in systems are, together with claim systems, the only area
where the airport baggage handling system and the customer interact.
The check-in systems must be of the highest quality and capable of
accommodating the special demands of both airports and customers in
an ever-changing industry.
BEUMER Group's CrisCheck® check-in conveyors integrate weighing and
labelling in a single, flexible system which meets all relevant
international safety standards. The floor-mounted frame features
integrated wheels for easy access and movement, whilst the modular
design offers a choice of belt types and widths. CrisCheck® can
easily be expanded or reconfigured as the airport adapts to changes
in future demand, thus offering a sustainable solution.
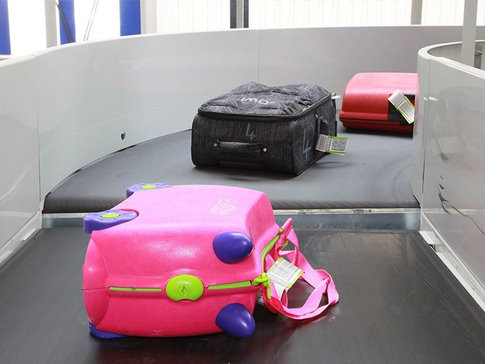
Baggage Conveyor Systems
-
The CrisBelt conveyor system combines cost-effective baggage
handling with reliable operation, easy maintenance and low energy
consumption.
The inherent flexibility of its modular design allows CrisBelt to
help airports of all sizes incl. major air-traffic hubs and regional
airports, to meet their objectives for cost-effective and reliable
baggage transport.
By combining standard, off-the-shelf modules with the flexibility to
specify features such as the belt width, belt type, drive locations
and inclines, CrisBelt provides a fast, easy and cost effective
transport system for carrying all types of baggage between the
arrival, transfer and departure baggage systems.
The modular approach enables the CrisBelt baggage conveyor system to
combine fast installation with robust, reliable and quiet operation
and a minimal spares inventory.
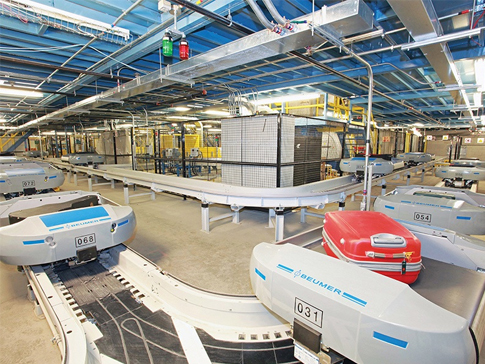
High Speed Transportation Systems
-
We design, build, and integrate high-speed baggage transport and
sortation systems. These high speed baggage handling systems play a
vital part in securing a fast and accurate transfer of baggage from
terminal to terminal for shorter connection times and optimised
passenger flow.
We offer the CrisBag® integrated tote system and the autover®
independent carrier system (ICS) as proven high-speed baggage
transport and sortation solutions.
Both systems achieve rates of 10 m/sec, which plays a vital role in
securing a fast and accurate transfer of baggage from terminal to
terminal in major airports around the world.
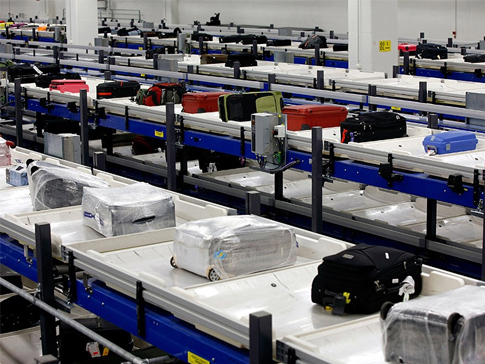
Early Baggage Storage systems
-
Early baggage storage (EBS) systems allows passenger bags to be checked in hours
before flight time with the flexibility of retrieving the bag automatically at
any time. An EBS system also manages peak volumes and reduces labour
requirements considerably.
We offer a wide range of solutions including CrisBag® line based EBS, CrisStore
racking solutions and traditional conveyor storage solutions.
Features of the CrisBag® line based EBS:
- Modular lift and CrisBag® lane system
- Warehouse for long time random storage
- Best and flexible use of building volume
- Manual retrieval for fallback
- Recirculation within EBS allow single bag access
Features of the CrisStore racking solutions:
- Modular system for easy configuration and expansion
- Storage in a choice of CrisBag® tote sizes
- Rack module height of under 3 m per module fits standard bag-room headroom
- Overall capacity configured to fit each airport
- 100% tracking and traceability
- Single bag access to individual items of baggage
Features of the traditional conveyor storage solutions:
- Simple and economical solution to early bag storage
- Evaluation of capacity, peak, volume and space is required
- Reduce of the overall electrical energy consumption
- Minimized risk of human error
- Ensures accuracy, efficiency and a more satisfying customer experience.
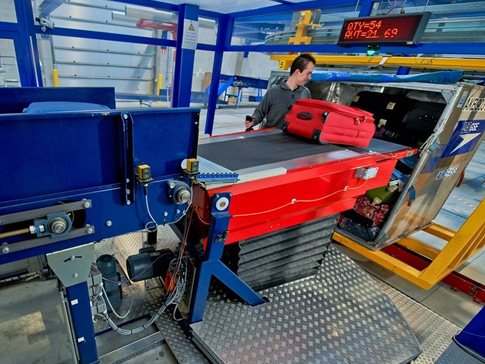
Make-Up Systems
-
AND UNLOADING SYSTEMS
We supply automated and semi-automated solutions as well as lifting
devices for loading and unloading of baggage in the make-up area.
Our loading and unloading solutions reduce costs, improve handling
efficiencies and provide a safer working environment for the ground
handling teams.
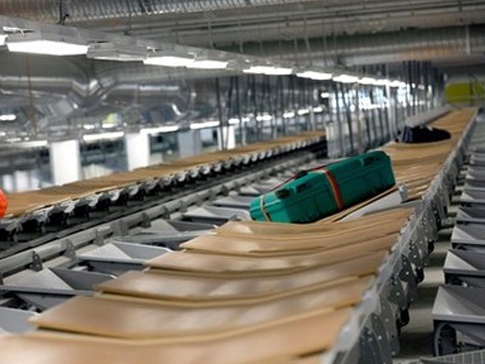
High Capacity Sortation Systems
-
We design, produce and install high-speed tilt-tray baggage
sortation systems that meet critical airport and airline needs. The
tilt-tray high-speed loop sorters feature the highest layout
flexibility with reduced installation and commissioning time. The
tilt-tray sorters are high capacity systems, which quickly and
accurately sort baggage to the right destination on time.
The high-speed baggage sortation line includes the energy-efficient
LS-4000E tilt-tray sorter as well as the LS-4000econ sorter.
The LS-4000 sorter family delivers real environmental benefits with
reduced carbon dioxide emissions and increased energy efficiency to
provide the lowest product life cycle cost (PLCC).
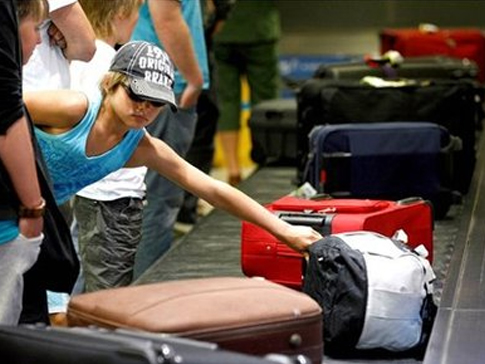
Reclaim systems
-
We design and integrate CrisClaim® carousels for smooth and quiet operation
implementing security and customs screening. The carousels offer high
flexibility and reliability under the extreme demands of high passenger density.
The CrisClaim® carousels are designed for smooth and quiet operation. The
CrisClaim® carousels offer high layout flexibility and reliability, exceptional
appearance and operation under the extreme demands of high passenger density.
As part of increased security in airports, we design and implement security and
customs screening of the bag before it is handed over to the passenger.
FACT SHEET:
- Customised modular concept in a sleek compact design
- Durable stainless steel construction
- Self-adjusting friction drives
- Minimised wear and tear
- Integrates perfectly into existing environment
- Smooth travel and low noise level
- Easy assembly, installation and maintenance
AT A GLANCE:
Technical data:
- Standard speed rate: 0.3-0.5 m/sec
- Static load: 350 kg per metre
- Dynamic load capacity: 240 kg per metre
- Maximum baggage length/width: 1200/750 mm
- Level change: Up to 12° incline/decline
- Noise level: max. 55 dBA
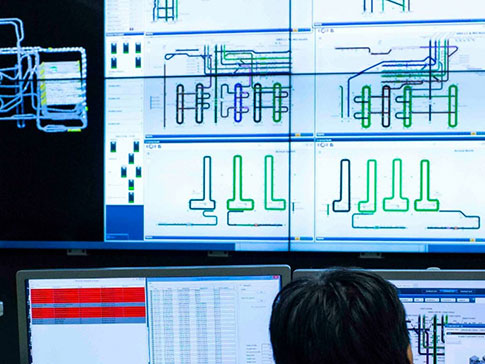
Airport - Software Suite
-
The BEUMER Group Airport Software Suite combines some of the
industry’s most advanced Baggage Handling System High Level Controls
(BHS HLC) with intuitive, web-based user interfaces to introduce new
levels of ease and efficiency to the baggage handling process.
The foundation of the Airport Software Suite is a set of proven,
standard controls modules. Each module implements advanced equipment
control assuring optimum availability and reliability.
The intuitive user interface graphically integrates all of the
software modules including those for peripheral equipment and
subsystems. This gives operators a complete set of widget-based data
on a virtual desktop, as well as secure access for operating and
controlling the entire baggage handling system.
Logistic systems
-
We have the experience - you enjoy the benefits.
As a global logistic systems development and integration leader
within conveying, loading, palletising, packaging, sorting and
distributing, we know all about goods and products that need
transporting, and we know exactly what is needed to transport them.
No logistic centres are alike and our solutions reflect this. By
carefully considering your specific business needs, we design, build
and integrate sortation and logistic systems to achieve your
objectives most efficiently and preferably even exceed your
expectations.
Our systems handle peaks with ease and are readily scalable to keep
pace with changing business requirements. With BEUMER Group, you get
a leading edge and seamless, cost-efficient operations - and a quick
return on Investment. 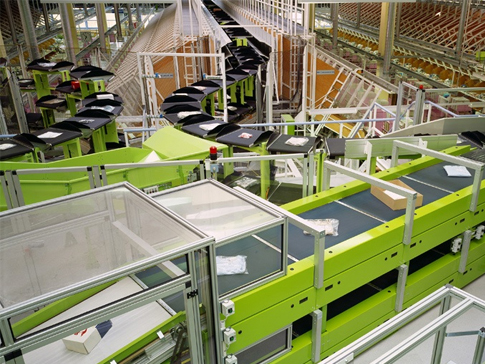
Cross-belt sortation systems
-
The BEUMER Group portfolio of cross belt sortation systems includes
the BEUMER Belt Tray Sorter and the Crisplant LS-4000CB Cross-Belt
Sorter. With a large number of installations worldwide, BEUMER Group
sortation equipment and software are critical components of today's
most sophisticated and highest throughput automated material
handling systems in various industries.
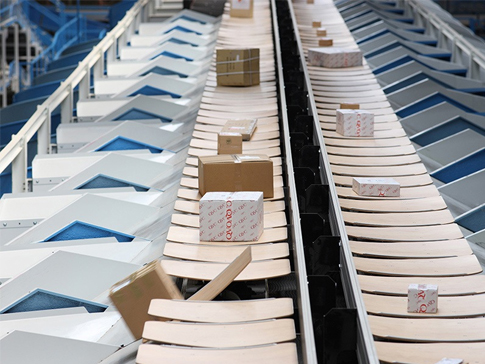
Tilt-tray sortation systems
-
The BEUMER Group portfolio of tilt tray sortation systems includes
the BEUMER Tilt Tray Sorter and the LS-4000E Tilt-Tray Sorter. With
a large number of installations worldwide, BEUMER Group sortation
equipment and software are critical components of today's most
sophisticated and highest-throughput automated material handling
systems.
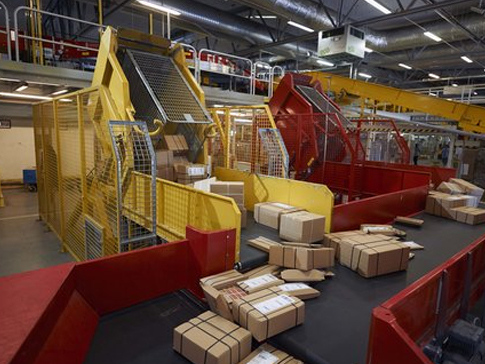
Conveying systems
-
BEUMER Group offers a full range of case- and pallet-handling
conveying systems and conveyor control systems for warehouses,
distribution centres, postal and parcel services and manufacturing
facilities worldwide.
Conveyors delivered by BEUMER Group are designed with performance,
durability and reliability in mind to meet the accumulation,
transportation, sortation and storage needs of virtually any
manufacturing or distribution environment.
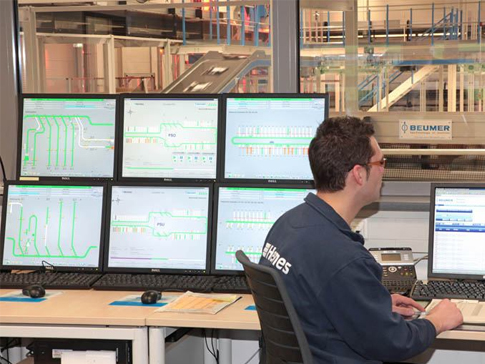
Sorter Controls
-
AT A GLANCE
BEUMER Group software controls is used for system-wide optimisation.
The ability to combine precise control of individual machines, with
system-wide visibility of work flows, allows the system to be
continually optimised to avoid bottlenecks and achieve faster
throughput and higher productivity.
BEUMER Group’s software system integrates three levels of controls:
- Embedded software on the controller boards for each sorter
- BEUMER Group Machine Controller system to keep track of items on the sorters including scanning information and sort positions
- BEUMER Group System Controller to adjust and optimise the sortation process for each individual sorter.
The system control can integrate with
- SCADA
- PLC controlled conveyors
- Barcode scanners
- Line sorters
- Conveyor belts
- Automatic print and apply stations
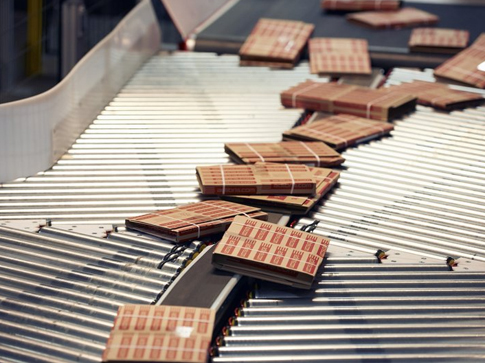
AUTOMATIC PARCEL SINGULATOR
-
The Automatic Parcel Singulator transforms a bulk flow of parcels
into a uniformly separated, spaced and aligned flow, before the
in-feed to the automated induction of a high-speed loop sorter.
The Automatic Parcel Singulator is able to handle a wide variety of
postal items and provides a single system for handling parcels,
flats, totes and sealed bags from the collection and distribution
sorting areas. Cyclical operation enables the Automatic Parcel
Singulator to adjust the speed of the parcel flow in response to
changing levels of demand at the induction to the sorting system. As
a fully automated system, the Automatic Parcel Singulator minimises
the need for manual handling and supervision during normal
operation.
FLEXIBLE AND LOW ENERGY CONSUMPTION
The Automatic Parcel Singulator features efficient use of available
space and optimised integration into a sorter induction for existing
loop-sorter systems. The Automatic Parcel Singulator is controlled
by PLC and frequency inverters capable of reusing kinetic energy
which enable the system to combine maximum capacity and throughput
with minimum energy consumption.
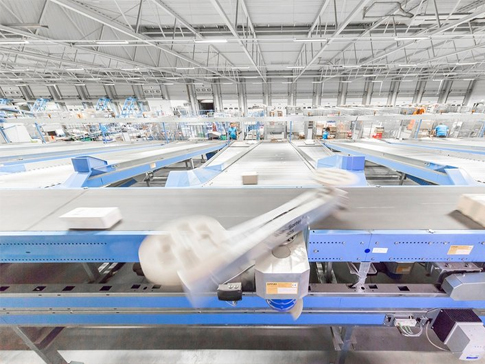
The Rota-Sorter
-
MORE PERFORMANCE, FLEXIBILITY AND ECONOMIC EFFICIENCY
An all-round performer in a class of its own
BEUMER Group's versatile machine with superior operational
efficiency. The Rota-Sorter can handle a vast range of items on a
single line at high speed. Its unique discharge technology makes
sortation extremely gentle while the system distinguishes itself
through its flexibility and economic efficiency.
An all-round sorter
The Rota-Sorter handles a great variety of items on a single line:
large, small, tall, flat, different weight categories and in
different packaging. High-speed operation up to 5,000 items per hour
on one line with a possibility to be expanded to up to three lines
above each other, makes if possible to achieve a maximum capacity of
15,000 items per hour.
Highlights
- Design as a single, double or triple sorter
- Capacity: mixed goods up to 15,000 items per hour
- Quick, reliable discharge
- Gentle item handling
- Flexible modular design
- Everything from one source
- Environmentally friendly due to high energy efficiency
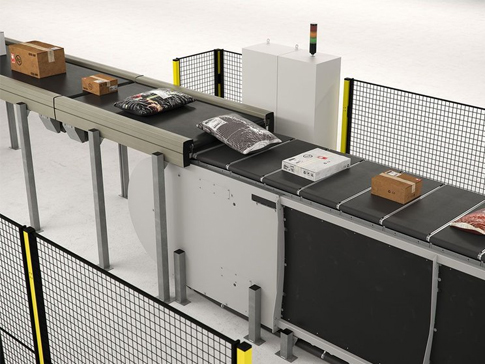
BG Line Sorter
-
Next-Generation Line Sorter Technology
The BG Line Sorter sets new benchmarks for mid-size-volume material
handling by combining the simplicity of a line sorter with the
handling capabilities of a high-speed cross-belt sorter.
The introduction of BEUMER Group’s unique slat-belt technology
enables the BG Line Sorter to extend the handling mix by sorting the
widest possible range of items whilst its modular design provides
the flexibility to optimise the use of space and ensure the
scalability to support future growth.
Highlights:
- Active slat-belt technology handling polybags, parcels, flats, totes, sacks, sealed bags, fragile and high-friction items
- Capacity: 1,500-10,000 items/hour
- Maximum item width: 800 mm (32”)
- Maximum item length: 1500 mm (59“)
- Maximum item weight: 25 kilos (55 lbs) single belt, 50 kilos (110 lbs) if occupying multiple belts
- Benefits:
- Modular design with high space efficiency and scalability
- Reliable and precise sortation across the widest mix of item shapes and sizes
- Easy installation with the scalability to meet future changes in capacity
- Low-friction components ensure endurance and high system availability
- Lower maintenance costs than conventional line sorters
Benefits:
- Modular design with high space efficiency and scalability
- Reliable and precise sortation across the widest mix of item shapes and sizes
- Easy installation with the scalability to meet future changes in capacity
- Low-friction components ensure endurance and high system availability
- Lower maintenance costs than conventional line sorters
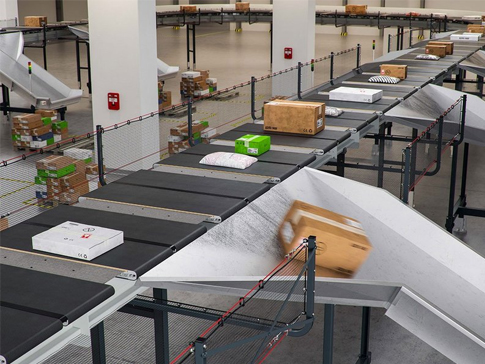
BG Sorter CB
-
New Generation Cross-Belt Sorter
The BG Sorter CB introduces innovative features which increase the
level of efficiency, throughput and flexibility for high-capacity
automated sortation.
A new full cross belt, contactless energy supply and real-time
wireless communications help to ensure the highest quality of
sortation and an extended handling mix. These features allow almost
all items to be handled through the automated system resulting in
higher efficiency and later cut-off times for customers.
The BG Sorter CB minimises Product Life Cycle Costs (PLCCs) due to
the reduced maintenance levels and operating costs delivered by its
energy-efficient technologies. The system also contributes to the
environmental sustainability and to an improved return on investment
(ROI).
Highlights:
- Sorter speed: Up to 3 m/sec (590 ft/min)
- Drive systems: OptiDrive or Linear Synchronous Motor (LSM)
- Power supply: Contactless energy supply
- Real-time wireless communication system
- Maximum item length: 1500 mm (59”) on one belt
- Maximum item width: 1000 mm (39.4”) on one belt
- Maximum item weight per carriage: 50 kg (110 lbs)
- Belt configurations per carriage: Single, double or triple belt
- Benefits:
- High-capacity sortation with the widest mix of items
- Highest possible availability and flexibility to optimise capacity
- Optimum sortation quality from real-time wireless communication
- Safe handling during induction with item monitoring
- Diagnostic tools and condition monitoring provide lower product life-cycle costs
Benefits:
- High-capacity sortation with the widest mix of items
- Highest possible availability and flexibility to optimise capacity
- Optimum sortation quality from real-time wireless communication
- Safe handling during induction with item monitoring
- Diagnostic tools and condition monitoring provide lower product life-cycle costs
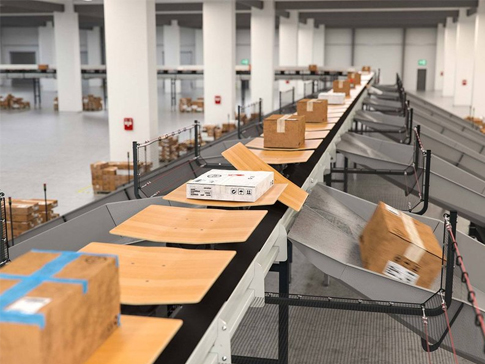
BG Sorter ET
-
New Generation Tilt-Tray Sorter
The BG Sorter ET is the innovative new generation tilt-tray sorter
from BEUMER Group.
A new closed-deck tray technology and real-time wireless
communications ensures the highest quality of sortation and safe
handling of items. These features allow almost all items to be
handled through the automated system resulting in higher efficiency
and later cut-off times for customers.
Highlights:
- Sorter speed: Up to 3 m/sec (590 ft/min)
- Drive systems: OptiDrive or Linear Synchronous Motor (LSM)
- Power supply: Contactless energy supply
- Real-time wireless communication system
- Maximum item length: 1000 mm (39.4”) single tray and 2000 mm (79”) spanning two trays
- Maximum item width: 1000 mm (39.4”)
- Maximum item weight per tray: 60 kg (132 lbs)
- Benefits:
- Highest possible availability and flexibility to optimise capacity
- Optimum sortation quality from real-time wireless communication
- Safe handling during induction with item monitoring
- Diagnostic tools and condition monitoring provide lower product life-cycle costs.
Benefits:
- Highest possible availability and flexibility to optimise capacity
- Optimum sortation quality from real-time wireless communication
- Safe handling during induction with item monitoring
- Diagnostic tools and condition monitoring provide lower product life-cycle costs
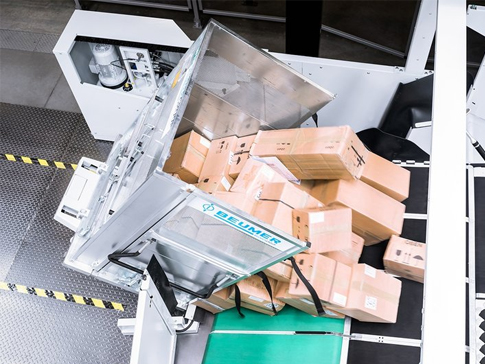
Parcel Picker
-
ERGONOMIC, SAFE AND ROBUST
Higher operational performance
Global competitive pressures in parcel logistics require constant process
optimisation. The BEUMER Parcel Picker® helps companies meet the growing
requirements by significantly increasing operational performance. The robust
BEUMER Parcel Picker® allows faster and more efficient unloading and a
consistently high throughput.
Easy and gentle unloading
The semi-automatic BEUMER Parcel Picker® is a fast and ergonomic solution for
unloading packages, parcels and shipping units of different weights and sizes.
The unloading unit works with swap bodies, fixed truck bodies and roller
containers and can easily be operated. The parcels are either pulled onto the
conveying system with an ergonomically designed, manually operated manipulator,
or - in case of roller containers – by adding a designated module. In both cases
the parcels are unloaded in bulk and transferred to the sortation system by a
telescopic belt conveyor.